AICHI METAL
Technical Case Studies
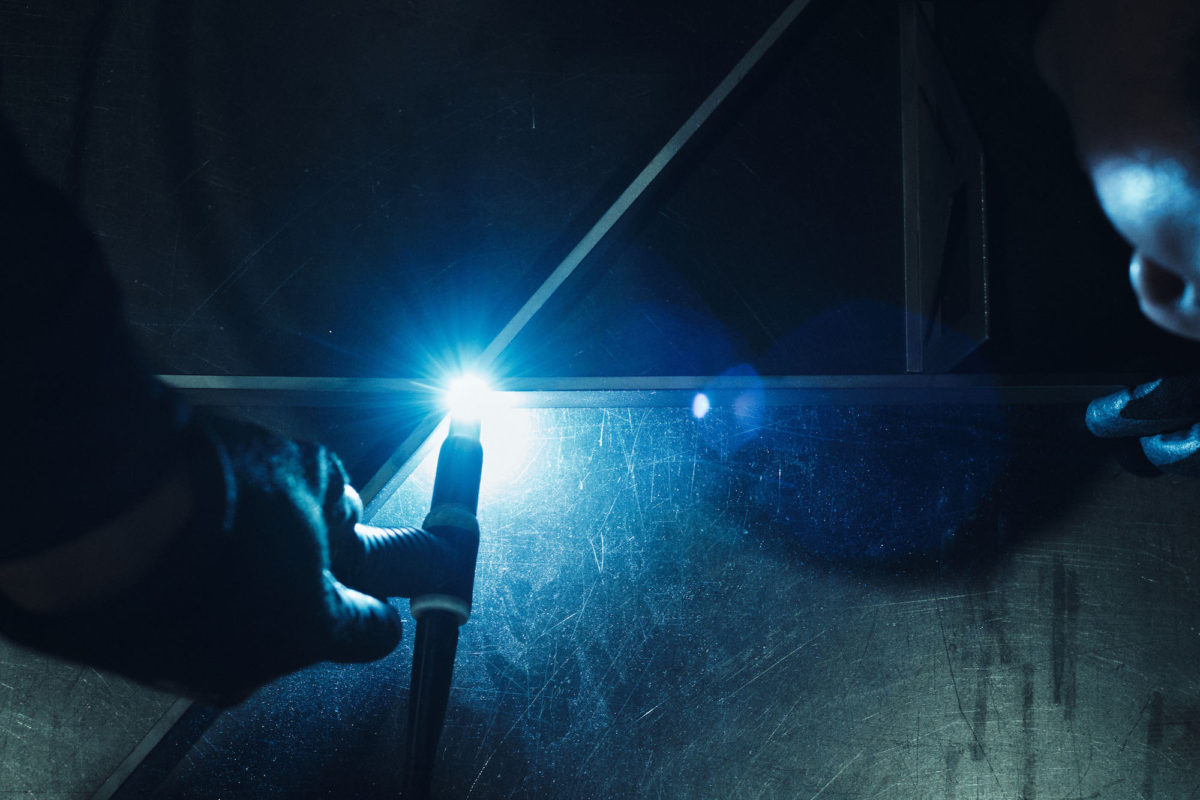
One chance led to a visit to Tsubame City in Niigata Prefecture, where a network was established with a number of companies commissioned to carry out advanced machining. It was mid-2020 when the first state of emergency was declared. The companies were receiving projects in fields such as semiconductors, robotics and energy, so the metal materials they were dealing with and the processing machines were of a different level. Whereas we focused on the hands of the craftsmen, the other side of the company’s operations focused on the know-how of the craftsmen. This is where we came across the term 4M management. This refers to how the four M’s = Man, Machine, Material and Method are managed and linked to quality. In the world of semiconductors, for example, once a process control method has been decided, it cannot be changed, down to the person processing, the processing machine or even a single processing tool. The ultimate traceability at the moment is required. However, this creates many contradictions in the way small and medium-sized enterprises (SMEs) are managed. It will be interesting to see how this is cleared up.
It’s all about dreams
In the field of small and medium-sized enterprises (SMEs), a variety of management know-how is used to generate profits. For example, the daily interaction between machines, people, time and delivery schedules is hectic and fluid, with priority given to work that can be done with available machines, work that can only be done by skilled people and work that cannot be done by skilled people, time spent in the morning, afternoon, evening and overtime, and delivery schedules brought forward to make time for new things. The exchange is anyway hectic and fluid. The more speedy this interaction goes, the more leeway it creates, and leeway often translates directly into revenue. However, 4M management does not allow this. The earnings of SMEs then become difficult to control all at once. On the other hand, however, the very act of being trained in 4M management has the potential to bring about tremendous improvements in corporate value. If revenue can be calculated based on the opposite interaction, the company’s responsiveness, breadth and level of know-how will clearly improve dramatically. However, there is no transitional period in 4M management, and when the time comes to place such an order, we have to do it. Now, in this context, I am thinking about the kind of interactions that would be possible if it were AICHI Metals, for example.
Essence
For example, we might be able to handle the ‘Man’ part. Naturally, there is a difference in quality between craftsmen. Especially when it comes to VeroMetal, one of our partners is a painting company that has been awarded No. 1 in Japan, and only this company can handle the quality. For example, when you order from us, all repeat orders are decided by such a company according to the quality you require, and the person in charge is fixed, so that more stable quality control can be achieved. On the other hand, the difficulty may be Method. In our case, the work is essentially handmade, so even if the finish looks all the same at first glance, there are subtle differences if you look at the details of the details. It is almost impossible to create exactly the same irregularities, especially when the decorative treatment creates unevenness across the entire metal surface. In these areas, there is no Method that creates exactly the same thing in the finish itself. One by one, the 4M management seems to leave room for a variety of responses, but it is no longer possible to control all four perfectly. However, it is almost certain that this perspective will live on in our management and workflow updates. We would like to add it to our own know-how as we pursue it little by little.