AICHI METAL
Technical Case Studies
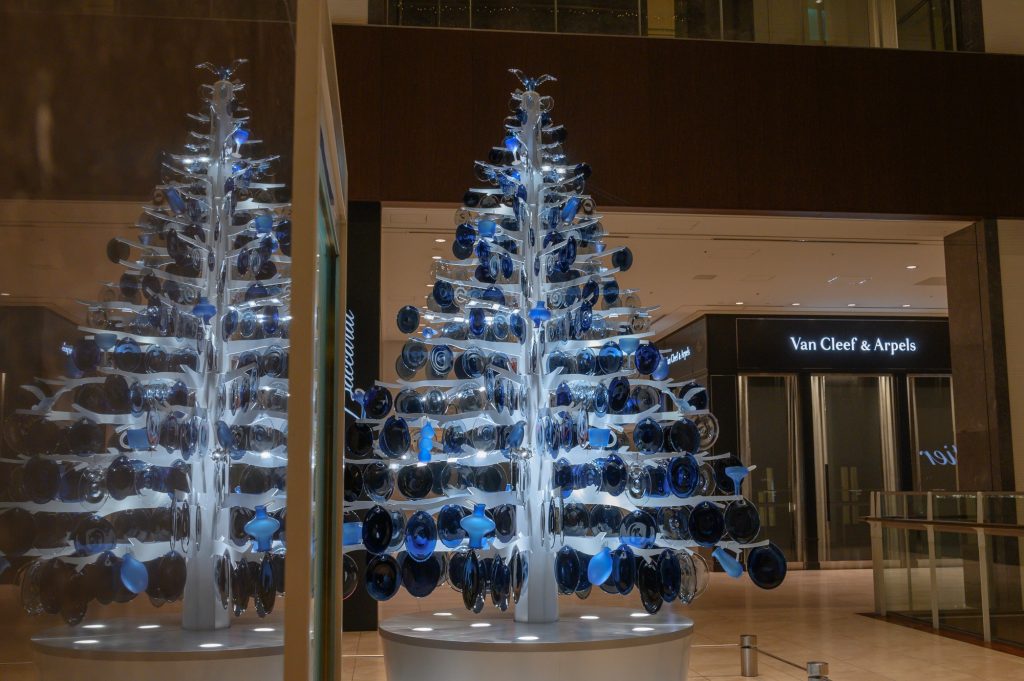
Art pieces are mysterious. For example, it does not make something useful or cure something just because it is there. In other words, it does not have the same functional benefits as a product. However, there are times when you get the experience of seeing the art piece and it changes the way you see the world in a way that you had been thinking about it. It may be that it changes the way you think, or that it changes the way you think itself. I believe this is due to the fact that the role of art is not about ‘function’ but about ‘information’. The art piece contains a vast amount of ‘information’ that an artist has arrived at, including a view of the world and society through an individual’s intellect. When this information reaches us through the work, it is combined with our thoughts as the recipient and may fuse together like a kind of chemical reaction to become new information. On the other hand, the work of AICHI METALS usually requires “”function”” first. Naturally, accidents must not occur or anyone must not be harmed. Furthermore, we must be able to accurately and deeply express the intentions of the designers and designers. The finish must be function-oriented, such that the intention of the design is not disrupted so that people can use the product without having to think about it. This is exactly the opposite of an art piece. This time, we had the very rare opportunity to undertake the production of a part of it.
Accuracy in support of ‘information’
The commission for this project came from Gallery Nao Masaki, a prominent gallery in Nagoya City, and the artist creating the work is Kanazawa-based glass artist Kazumi Tsuji. The spatial director was Nao Masaki of Gallery Nao Masaki. The installation took place at Midland Square in front of Nagoya Station, during the Christmas 2020 event. AICHI METALS was responsible for the production of the tree’s support, as well as the welding and painting of the branches and pots. The part we produced this time was the tree part of the Christmas tree, from which 400 glass dishes were suspended. The total weight of the plates alone is about 1 tonne. The tree trunk has to be strong enough to support this weight. On the other hand, a rugged finish would reduce the completeness of the artwork as a whole. What we have understood from our exposure to art piece production is that, first of all, the people involved in art have the ideas and experience to realise ‘functional excellence’. This is something we have come into contact with on a daily basis and the chemistry was excellent. The trunk finish is white-coloured and thermal spraying techniques are used to preserve the surface beauty. The final combination with the branches, for which component fabrication was carried out by another company, is the on-site finish. As is usually the case on site, the pieces were assembled one by one by staff from the site installation/construction department to complete the project.
The wonder of presence
During the event, our staff visited the venue many times, as it is close to AICHI METALS. It was very impressive to see so many people visiting and taking photos. All the vessels on display were sold out. It was a very significant event. The main focus of the work this time was on the vessels, with the tree itself playing a supporting role, so to speak. This stance is the same as all the metal components we usually work with and deliver, but the presence of the art piece gave us the strange impression that we were standing on a different stage from the usual existence of metal components themselves. Responding with solid quality. To understand the project as a project accurately and in depth. This project brought a completely new experiential value to us, even though it is all common to our everyday work. The sight of the public looking at the metal components together for the purpose of this work was like one reward for our usual work, for which we are also deeply grateful to all those involved.